|
Production costs have their own classification, divided in relation to how they "behave" when production volumes change.
Costs related to different types behave differently.
Fixed costs (FC, TFC)
Fixed costs, as the name suggests, are a set of enterprise costs that arise regardless of the volume of manufactured products.
Even when the enterprise does not produce (does not sell or does not provide services) anything at all. To designate such costs,
the abbreviation TFC (time-fixed costs) is sometimes used in literature. Sometimes, simply FC (fixed costs) is used.
Examples of such costs can be the monthly salary of an accountant, rent for premises, land rent, etc.
It should be understood that fixed costs (TFC) are, in fact, conditionally constant. To a certain extent, they are still affected by production volumes.
Let's imagine that a machine-building plant has an automatic chip and waste removal system installed in its workshop. With an increase in the volume
of manufactured products, it would seem that no additional costs arise. But when a certain limit is exceeded, additional equipment maintenance,
replacement of individual parts, cleaning, and elimination of current faults that will occur more often will be required.
Thus, in theory, fixed costs (expenses) are actually such only conditionally.
That is, the horizontal line of costs (expenses) in the book is not such in practice. Let's say that it is close to some constant level.
Accordingly, in the diagram (see below), such costs are conditionally shown as a horizontal TFC graph
Variable production costs (TVC)
Variable production costs, as the name suggests, are a set of enterprise costs that directly depend on the volume of manufactured products.
In literature, this type of cost is sometimes referred to by the abbreviation TVC (total variable costs). As the name suggests, “variable” means
increasing or decreasing simultaneously with the change in the volume of products manufactured.
Direct costs include, for example, raw materials and materials that are part of the final product or are consumed in the production process
in direct proportion to its load. If an enterprise produces, for example, cast blanks, then the consumption of the metal from which these blanks
are made will directly depend on the production program. The term “direct costs (expenses)” is also used to denote the expenditure of resources
that are directly used to manufacture a product. These costs are also variable costs, but not exclusively, as this concept is broader. A significant
part of production costs is not directly included in the product but changes in direct proportion to the volume of production. Such costs include,
for example, the costs of energy resources for the operation of production equipment directly involved in the production of goods.
It is necessary to take into account that a number of costs for resources used by an enterprise must be separated for the purposes of classifying
costs. For example, electricity used in heating furnaces of a metallurgical enterprise is related to variable costs (TVC), but another part of the
electricity consumed by the same enterprise for lighting the territory of the plant is already fixed (TFC). That is, the same resource consumed
by an enterprise can be divided into parts that can be classified differently - as variable or as fixed costs.
There are also a number of costs, the costs of which are classified as conditionally variable. That is, they are associated with production
processes, but do not have a directly proportional relationship with production volumes.
In the diagram (see below), variable production costs are shown as a TVC graph.
This graph differs from the linear one, which it theoretically should be. The fact is that with sufficiently small production volumes, direct production
costs are higher than they should be. For example, a casting mold is designed for four castings, but you produce only two. You load the melting
furnace below its design capacity. As a result, more resources are spent than the technological standard.
After a certain production volume is exceeded, the schedule of variable costs (TVC) becomes close to linear. However, when production surpasses
another threshold, the costs per unit of output begin to increase again. This is because, when the normal level of the enterprise’s production
capabilities is exceeded, more resources must be spent on the release of each additional unit of output. For instance, paying workers overtime,
spending more on equipment repairs (under irrational operating conditions, repair costs grow geometrically), and other similar expenses.
Therefore, variable costs are considered to follow a linear schedule only conditionally, within a certain range, corresponding to the normal
production capacity of the enterprise. Beyond this range, the costs deviate from linearity due to inefficiencies and additional resource expenditures.
Total costs of the production (TC)
Total costs of the production are the sum of variable and fixed costs. In the literature, they are often referred to as TC (total costs).
That is,
TC = TFC + TVC
where costs by type:
TC - total
TFC - fixed
TVC - variable
In the diagram, total costs are reflected by the TC graph.
Average fixed costs (AFC)
Average fixed costs are the quotient of dividing the sum of fixed costs per unit of output. In the literature,
this value is referred to as AFC (average fixed costs).
That is,
AFC = TFC / Q
where
TFC - fixed production costs (see above)
Q - quantity (volume) of production
The meaning of this indicator is that it shows how many fixed costs are per unit of output. Accordingly, as the volume of production grows,
each unit of the product accounts for a smaller share of fixed costs (AFC). Accordingly, a decrease in the amount of fixed costs per unit
of production (services) of the enterprise leads to an increase in profit.
In the diagram, the value of the AFC indicator is displayed by the corresponding AFC graph
Average Variable Costs (AVC)
Average variable costs are the quotient of the sum of the costs of producing products (services) by their quantity (volume).
They are often designated by the abbreviation AVC (average variable costs).
AVC=TVC / Q
where:
- TVC - variable production costs (see above)
- Q - quantity (volume) of production
It might seem that, when calculated per unit of production, variable costs should always be the same. However, for the reasons discussed
earlier (see TVC), production costs fluctuate per unit of output. Therefore, for approximate economic calculations, the value of average
variable costs (AVC) is taken into account for volumes close to the normal capacity of the enterprise.
In the diagram, the dynamics of the AVC indicator is shown by a graph with the same name.
Average Costs (ATC)
Average costs of an enterprise are the quotient of the sum of all costs of the enterprise by the amount of output (work, services).
This value is often referred to as ATC (average total costs). The term “total cost per unit of production” is also used.
ATC=TC / Q
where:
- TC - total (general) costs (see above)
- Q - quantity (volume) of production
It should be noted that this value is only suitable for very rough calculations, calculations with minor deviations in the volume
of production, or with an insignificant share of fixed costs in the total cost of the enterprise.
With an increase in production volumes, the calculated value of costs (TC), obtained based on the values of the ATC indicator
and multiplied by the volume of production, other than the calculated one, will be greater than the actual one (costs will be overstated),
and with a decrease, on the contrary, they will be understated. This will occur due to the influence of conditionally fixed costs (TFC). Since
TC=TFC+TVC, then:
ATC=TC / Q
ATC= ( TFC+TVC ) / Q
Thus, when production volumes change, the value of fixed costs (TFC) will not change, which will lead to the error described above.
Dependence of Types of Costs on the Level of Production
The graphs show the dynamics of the values of various types of costs depending on the volume of production at the enterprise.
These graphs illustrate how different costs behave as production scales up or down, highlighting the non-linear nature of
cost behavior in real-world scenarios.
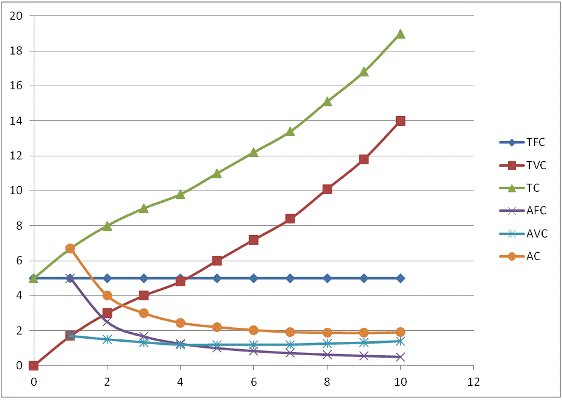
Marginal Costs (MC)
Marginal costs are the additional costs required to produce each additional unit of output.
They are often referred to by the abbreviation MC (marginal costs).
MC= ( Q2−Q1) / ( TC2−TC1 )
where:
- TC - total costs
- Q - quantity (volume) of production
From the formula above, it is clear that MC for each additional unit of output will be equal to
AVC (average variable costs) over the interval ([Q1; Q2]).
Since
TC=TFC+TVC, then:
MC = ( Q2−Q1 ) / ( TC2−TC1 )
MC = ( Q2−Q1 ) / ( ( TFC+TVC2 ) − ( TFC + TVC1 ) )
MC = ( Q2 − Q1 ) / ( TVC2−TVC1 )
Thus, marginal costs are exactly equal to the variable costs required to produce additional output.
If we need to calculate MC for a specific production volume, we assume that the interval we are dealing with is ([0; Q])
(from zero to the current volume). At “point zero,” variable costs are zero, and production is also zero, simplifying the formula to:
MC=TVCQ / Q
where:
- TVCQ is the variable costs required to produce (Q) units of output.
Importance of Marginal Costs
Understanding marginal costs is crucial for businesses as it helps in determining the optimal level of production.
By analyzing MC, companies can decide whether producing an additional unit of output is profitable.
If the marginal cost of producing one more unit is lower than the price at which it can be sold, the company can increase its profit
by expanding production.
Practical Applications
In practice, marginal costs are used in various economic and business decisions, such as:
- Pricing Strategies: Setting prices based on the cost of producing additional units.
- Production Planning: Determining the most cost-effective level of production.
- Cost Management: Identifying areas where costs can be reduced by optimizing production processes.
By carefully monitoring and managing marginal costs, businesses can improve their efficiency and profitability.
Fundamentals of Economic Analysis |
Описание курса
| Type of Costs. Calculation example
|