Организация ремонта оборудования
Расчет длительности межремонтного цикла для легких и средних металлорежущих станков
Расчет длительности межремонтного цикла для легких и средних металлорежущих станков осуществляется по формуле:
24 000 – нормативный ремонтный цикл, станко-часы.
Вп – коэффициент, который учитывает тип производства (для массового и крупносерийного производства он равняется 1,0, для серийного - 1,3, мелкосерийного и единичного -1,5).
Вм – коэффициент, который учитывает обрабатываемый материал (при обработке конструкционных сталей он равняется 1,0, для чугуна и бронзы – 0,8, для высокопрочных сталей – 0,7).
Ву – коэффициент, который учитывает условия эксплуатации оборудования (при нормальных условиях механических цехов он равняется 1,0, в запыленных и с повышенной влажностью – 0,7).
Вс – коэффициент, который отображает группу станков (для легких и средних станков он равняется 1,0).
Определение длительности межремонтного периода
Определение длительности межремонтного периода определяется по формуле:
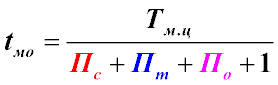
П0 – количество осмотров во время межремонтного цикла.
Пс –количество средних ремонтов в течении межремонтного цикла.
Пт – количество текущих ремонтов в течении межремонтного цикла.
Исходя из этого, длительность межремонтного цикла может быть определена по формулам:
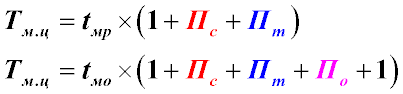
Тм.ц – длительность межремонтного цикла
П0 – количество осмотров во время межремонтного цикла.
Пс –количество средних ремонтов в течении межремонтного цикла.
Пт – количество текущих ремонтов в течении межремонтного цикла.
Годовой объем ремонтных работ
Общий годовой объем ремонтных работ определяется по формуле:

Тк, Тс, Тт, Т0 – суммарная трудоемкость (слесарных, станковых и других работ) капитального, среднего, текущего ремонтов и осмотров на одну единицу ремонтной сложности. Измеряется в нормо-часах.
Ri – количество единиц ремонтной сложности на i-тую единицу оборудования (механической части). Измеряется в ремонтных единицах.
Спр.i. – количество единиц оборудования i-того наименования, штук.
Если объем работ определяется отдельно по видам работ (слесарные, станковые и другие), то на одну ремонтную единицу используются соответствующие нормы времени по всем видам планово-предупреждающих ремонтов.
Расчет годового объема работ по межремонтному обслуживанию находится по формуле:
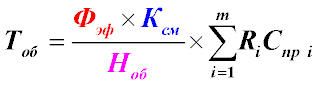
Фэф – годовой эффективный фонд времени работы одного рабочего. Измеряется в часах.
Ксм – сменность работы оборудования, которое обслуживается.
Ноб – норма обслуживания в смену на одного работника. Измеряется в ремонтных единицах.
Расчет численности персонала для ремонтных работ
Расчет численности работников, необходимых для ремонтных работ (Рсл) и межремонтного обслуживания (Р'сл), производится по видам работ:
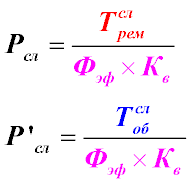
Т сл рем – трудоемкость слесарных работ для выполнения ремонтных работ
Т сл об – трудоемкость слесарных работ для межремонтного обслуживания.
Измеряются в нормо-часах.
Кв –коэффициент выполнения норм времени.
По аналогии проводится расчет численности межремонтного и ремонтного персонала по станковым и другим видам работ.
Расчет необходимого количества единиц оборудования (станков) (Спр) по межремонтному и ремонтному обслуживанию осуществляется по формуле:
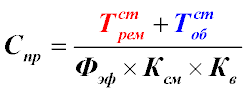
Т ст рем – трудоемкость станковых работ для выполнения ремонтных работ.
Т ст об – трудоемкость станковых работ для межремонтного обслуживания.
Измеряется в нормо-часах.
Фэф – годовой эффективный фонд времени работы за одну смену одного станка. Измеряется в часах.
Расчет потребности в материалах для ремонта
Расчет нужд цеха в материалах для ремонта проводится по формуле:

γ – коэффициент, который учитывает затраты материала на один капитальный ремонт оборудования на одну ремонтную единицу.
∑Rк, ∑Rс, ∑RТ – сумма ремонтных единиц агрегатов, которые подвергаются в течении года капитальному, среднему и текущему ремонтам.
L – коэффициент, который характеризует соотношения нормы затрат материала при среднем и капитальном ремонтах.
В – коэффициент, который характеризует соотношения нормы затрат материала при текущем и капитальном ремонтах.
Нормы запаса однотипных деталей для группы однотипного оборудования определяются по формуле:
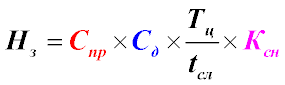
Спр – количество однотипных единиц оборудования, штук.
Сд – количество однотипных деталей в данном типе оборудования, штук.
Тц – длительность цикла изготовления партии однотипных деталей, который зависит от их количества в одно-модельных агрегатах (берется с практических данных главного механика предприятия).
Максимальный запас не должен превышать трехмесячных затрат сменных деталей одного наименования.
Фотография рабочего времени |
Описание курса
| Стратегическое управление организацией
|